- Case Study
- Peristaltic pump solutions from WMFTS are enabling a water treatment plant (WTP) at Cornish Metals’ South Crofty tin mine to bring sustainable benefits to the local environment
- Eight Bredel 40 hose pumps are transferring sludge at the WTP; during one stage of the process, the pumps transfer sludge up a height of 10 metres
- Three Qdos chemical metering pumps reliably dose hydrogen peroxide to oxidise the contaminated metals in the minewater at the WTP
Peristaltic pumps bring sustainability benefits to mine’s water treatment plant
When metal-rich, contaminated minewater enters rivers it damages the ecology by reducing fish populations and the diversity of invertebrates. As well as damaging biodiversity, polluted riverways also have a negative economic impact on tourism and leisure activities.
But a water treatment plant (WTP) at a mine site, like the one at South Crofty tin mine in Cornwall, England, pumps up minewater from underground shafts and decontaminates it before discharging the water into a nearby river.
Cornish Metals Inc. is working to reopen South Crofty, which ceased producing tin in 1998, by the end of 2026. To fully dewater the mine, approximately 8 million cubic metres of water will need to be pumped and treated to a standard set by the environment agency.
Cornish Metals is using eight Bredel 40 hose pumps and three Qdos chemical metering and dosing pumps from Watson-Marlow Fluid Technology Solutions (WMFTS) for vital roles at its South Crofty WTP.
Reliable, low-maintenance pumps
Three Qdos 120 pumps are accurately dosing hydrogen peroxide during the cleaning of contaminated minewater, to oxidise the metals and cause iron and arsenic to precipitate out of the solution, in the first of five process steps at the WTP.
Bredel hose pumps provide reliable, low maintenance and contained transfer of thick sludge (containing contaminants such as iron, manganese and arsenic) which is separated from the treated water in stages two and four. The Bredel Pumps transfer excess sludge from Lamella calrifiers, into a holding tank, from which a further Bredel pump pumps the sludge into a Deep Cone Thickener (DCT). The thickened sludge from the underflow of the DCT is pumped by a final Bredel pump into a holding tank, prior to disposal at a nearby tailing storage facility. In future years it is planned that the sludge will be disposed of with tailings in the form of paste fill in the underground voids of the mine.
Steven Kingstone, South Crofty Project Manager at Cornish Metals, said: “The main thing for us is the pump is running 24 hours a day. It's reliable, and it's ensuring that we've got containment of the chemicals. Hydrogen peroxide is quite a dangerous chemical. We need to ensure we've got good containment of that chemical and we've got reliability of the system, and that’s why we use the Qdos pump.
“Sludge density varies during the day, so we needed a pump that's going to manage that variable nature of the sludge. In the first stage of the process, the Bredels are pushing the sludge up around about 10 meters altogether. The final Bredels are pushing the thickened sludge up seven metres into the sludge holding tank. That's a very thick sludge, so those Bredel pumps are having to work quite hard.
“But again, the main thing is reliability. Ease of maintenance is also important. One of the advantages of the Bredel pump is the hose replacement on it is really quite simple compared to some of the other peristaltic pumps on the market.”
Cornish Metals expects dewatering of South Crofty to take 18 months. Once complete, the WTP will be used to manage the ongoing minewater treatment.
Sustainability benefits
Bredel and Qdos pumps are contributing to the WTP’s goal of minimising South Crofty’s impact on the local environment. Before start-up of the WTP, the Red River received untreated minewater as a legacy of past mining activities. A cleaner and healthier Red River will benefit people, wildlife and the local economy. Untreated minewater which leaks into local waterways can have damaging repercussions, such as when over 10 million gallons of heavily contaminated water flowed from the disused Wheal Jane tin mine (nearby to South Crofty), and caused serious pollution to a river and estuary in 1992.
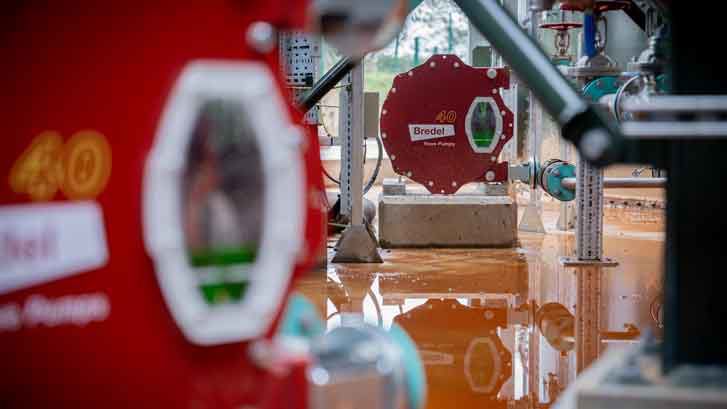
Bredel hose pumps in place at South Crofty tin mine
Kingstone said: “Environmentally, the biggest impact is the Red River historically has taken a lot of contaminated water from various mines in the area. The Red River has historically always been called Red River because, for hundreds of years it's run red with the mineral processing in the area. The mines all discharge through the adit system that underlies Camborne and Redruth. It contains a lot of metals and a lot of that was coming from South Crofty after its closure in 1998.
“But by treating the water now, before we discharge it back underground into the adit system, is a very positive impact on the quality of the water in the Red River downstream of Crofty. It has led to drops in iron of around about 99%, arsenic of 95%, compared to the untreated minewater, so that water in the river is becoming much clearer. It’s a much better quality of water that's ultimately being discharged on a bathing beach down at Gwithian.
“By removing those metals from the environment, it massively improves the quality of the water, and allows life to come back into the river.”
An added sustainability benefit of the South Crofty tin mine is the renewable energy the WTP generates. Water discharged from South Crofty powers a hydro-turbine that generates up to 15% of the power consumed by the WTP.
Kingstone said: “When the water is discharged into the adit system that underlies the mine, it goes down a shaft which drops the water around 50 metres. We’ve installed two turbines in the shaft, so that when the water goes through those turbines it generates 15% of the electricity used in the water treatment process, which is around 70 kilowatts per hour.”
Using a local supplier was also important for Cornish Metals.
Kingstone added: “We are lucky in Cornwall to have a number of suppliers such as Watson-Marlow, producing high quality equipment that we can utilise in the reconstruction of South Crofty mine. As the site develops, we look forward to continuing to work with Watson-Marlow.”
South Crofty, which first started production in 1592 and continued until 1998, has the fourth highest grade tin mineral resource globally, according to Cornish Metals. Tin connects almost all electronic and electrical infrastructure, making it critical to the clean energy transition.
Solutions for you
To learn more about our solutions for your applications please